Aerospace Parts Demand Precision
Aerospace components are among the most demanding in modern manufacturing. Each part must meet exacting standards for performance, safety, and reliability—often under extreme conditions. From turbine blades to lightweight structural supports, there’s no room for error. This is why CNC machining has become a go-to solution in the aerospace industry.
CNC machining aerospace projects require a blend of material knowledge, machine capability, and process control. The right CNC setup helps manufacturers consistently produce parts with tight tolerances and superior surface finishes. This article explains why CNC machining works well for aerospace parts and how to choose the right machine for the job.
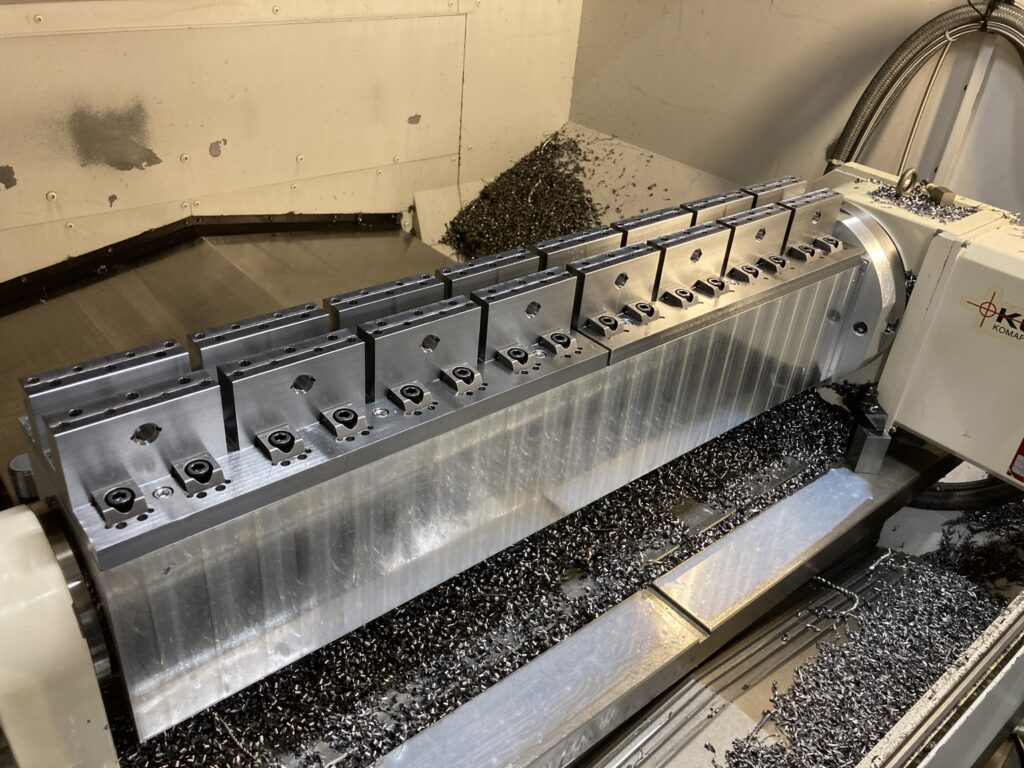
The Role of CNC Machining in Aerospace Manufacturing
CNC machining is essential in aerospace manufacturing because of its repeatability, accuracy, and flexibility. Whether producing engine mounts, brackets, or housings, CNC machining aerospace components allows for precise control over every dimension.
The aerospace industry uses a wide range of metals, including aluminum, titanium, and nickel alloys. CNC machines cut these materials into complex shapes while meeting strict needs for weight, strength, and heat resistance. CNC machining provides the consistency and quality needed for critical aerospace parts.
Key Aerospace Materials and How CNC Machines Handle Them
Tough materials are one of the biggest challenges in CNC machining for aerospace. Titanium, for example, is known for its strength and corrosion resistance, but it can also be tough on tooling. Inconel, another common aerospace alloy, requires slower cutting speeds and specialized tools due to its hardness and heat resistance.
High-performance CNC machines are built to handle these challenges. Strong frames, fast spindles, and good cooling help keep tolerances tight and tools lasting longer. Material knowledge and machine selection go hand-in-hand to ensure the process remains stable, accurate, and cost-effective.
Matching CNC Machine Type to Part Geometry
Aerospace parts are rarely simple blocks. They often feature complex contours, deep cavities, and multiple faces that must be machined in a single setup. This is where 5-axis machines shine. For many 5-axis CNC aerospace jobs, multi-angle capability reduces repositioning and improves accuracy.
Three-axis machines may be sufficient for simple brackets or flat panels, but when a part has complex geometry or critical dimensions across multiple planes, 5-axis machining is the clear choice. By machining more features in fewer setups, 5-axis equipment also reduces the risk of misalignment and helps maintain tighter tolerances.
Aerospace Tolerances: What Really Matters
Aerospace tolerances often push the limits of what a machine can hold. Structural parts may require ±0.005 inches, while critical engine components or sealing surfaces might need tolerances of ±0.0005 inches or better.
These aerospace tolerances aren’t just about hitting numbers—they ensure that assemblies fit together properly, operate safely, and last longer in extreme environments. Maintaining these tolerances requires not just the right machine, but also attention to temperature control, tooling condition, and real-time inspection.
In CNC machining aerospace projects, the cost of getting tolerances wrong can be enormous. Scrap rates, delays, and safety risks all increase when precision isn’t prioritized.
Factors to Consider When Sourcing an Aerospace Machining Partner
Choosing the right aerospace machining company is just as important as choosing the right machine. Your partner should have experience with CNC machining aerospace components, particularly those made from advanced materials or requiring complex setups.
Look for certifications like AS9100 and ITAR, as well as in-house quality control systems. Ask about their inspection equipment, software, and ability to trace part history. Also consider how they manage process validation and first article inspections.
A strong aerospace machining partner doesn’t just deliver parts—they help you reduce lead time, improve consistency, and avoid production headaches.
Why CNC Machining Aerospace Projects Need Specialist Attention
CNC machining aerospace work isn’t routine. From design collaboration to post-processing, it requires communication, planning, and traceability at every stage.
The right shop understands these pressures and has systems in place to keep projects moving smoothly. They’ll flag manufacturability issues early, provide design feedback when needed, and maintain detailed records to support compliance and quality audits.
Choosing a supplier who treats aerospace work with the care it deserves ensures a higher level of confidence in your supply chain and a lower risk of delays or defects.
Is Your CNC Supplier Ready for Aerospace Work?
Aerospace parts call for more than general machining. They require advanced equipment, material expertise, and an obsession with detail. If your current partner isn’t meeting the mark, it might be time to rethink your approach.
At Krukemeier, we specialize in CNC machining aerospace parts with the accuracy and accountability our customers expect. From first cut to final inspection, we’re committed to helping you deliver safe, reliable, and high-performance components.
If you’re working on your next aerospace project and need a machining partner who understands the stakes, we’re here to help.