Precision Machining for Complex Parts
When it comes to producing parts with intricate shapes and ultra-tight tolerances, conventional machining doesn’t always cut it—literally. That’s where wire EDM steps in, offering higher accuracy, better surface finishes, and less mechanical stress on the part.
Wire EDM, short for wire electrical discharge machining, allows manufacturers to remove material with extreme precision, without physically touching the part. Instead of cutting with blades or tools, wire EDM uses controlled electrical discharges to erode the metal.
The result? Sharp corners, narrow slots, and consistent performance—especially when working with hardened metals or complex geometries. Whether you’re building aerospace brackets or surgical components, wire EDM offers the precision and reliability your project demands.
In this article, we’ll explain how the process works, where it shines, and why it’s a core capability at Krukemeier.
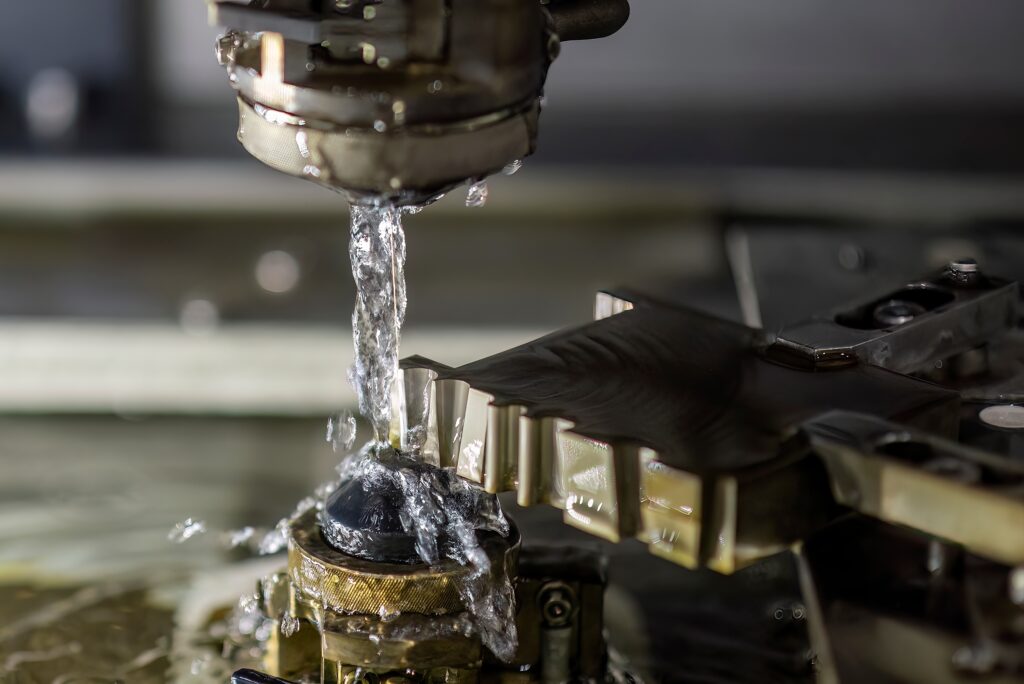
How Wire EDM Works in a Modern EDM Machine Shop
In a modern EDM machine shop, precision is everything. That’s why it plays such a critical role in delivering complex parts that meet exacting specifications.
Here’s how it works: a spool of thin wire—usually brass or copper—is stretched between two guides. The workpiece is submerged in a dielectric fluid, which helps control the electrical discharge and flush away debris. As the wire moves along a programmed path, a high-frequency electrical current passes between the wire and the part. Tiny, controlled sparks jump from the wire to the material, vaporizing it without ever making contact.
Because there’s no cutting force or tool pressure, wire EDM can handle delicate features and thin walls without risk of distortion. It also eliminates issues like burrs or tool wear, common in traditional machining. This makes it especially useful for parts made from hardened tool steel, titanium, or exotic alloys.
At Krukemeier, our EDM machine shop is equipped to work with challenging materials and complex geometries. We rely on this process when customers need high-performance parts that standard CNC machines just can’t deliver.
The Benefits of Wire EDM
Wire EDM stands out for its ability to deliver precision that traditional machining methods often can’t match. One of the most important advantages is its capability to hold extremely tight tolerances—often down to ±0.0001 inches—without introducing mechanical stress or heat distortion.
Because there’s no direct contact between the wire and the workpiece, there’s also no tool pressure to deform thin walls or small features. That makes wire EDM especially useful for delicate or high-detail parts that would be challenging to produce with standard milling or turning.
Another key benefit is the surface finish. Wire EDM cuts are clean, smooth, and burr-free, often eliminating the need for additional finishing processes. This saves time and helps maintain the integrity of the part—especially critical in medical or aerospace applications.
Finally, wire EDM is highly effective at cutting hardened materials. Instead of needing to machine a part before heat treating it (which can cause warping), you can machine the part after it’s been hardened, maintaining stability and reducing lead time.
Whether you’re prototyping a one-off component or running a short production batch, the reliability and repeatability of wire EDM make it a smart choice.
Understanding Wire EDM Tolerances and Precision Capabilities
When designing high-performance components, tolerances are everything. Even the smallest deviation can cause problems in assembly, functionality, or product life.
Wire EDM excels at holding incredibly tight dimensional limits. In many cases, tolerances down to ±0.0001 inches are achievable. That level of precision makes it ideal for components that require tight fits, complex shapes, or internal features that can’t be machined using traditional tools.
Consistent wire EDM tolerances also mean consistent parts—from the first to the last in a production run. There’s no tool wear or cutting force to introduce variability over time. That stability gives engineers and buyers confidence, especially when parts are headed into mission-critical systems like aircraft assemblies or surgical instruments.
At Krukemeier, we work with customers who need precision on every job. By leveraging wire EDM tolerances, we’re able to meet those expectations while reducing the need for secondary machining or manual finishing.
Industries That Rely on Wire EDM
Across many industries, precision isn’t optional—it’s essential. That’s why wire EDM has become a go-to process for manufacturers in sectors where part quality, tolerance, and complexity are non-negotiable.
Aerospace
In aerospace, components often need to withstand extreme temperatures, vibrations, and pressure. Wire EDM is used to cut intricate shapes in hardened alloys while maintaining exact tolerances. It’s ideal for engine parts, brackets, and structural supports that require both strength and precision.
Medical
Medical manufacturers also rely heavily on tight tolerances. From surgical instruments to implantable devices, parts must meet tight specs and leave no room for burrs or surface imperfections. Wire EDM delivers the clean edges and repeatability that those applications demand.
Defense
Defense contractors use wire EDM to create high-performance parts for weapons systems, vehicles, and electronics enclosures. The process offers both the accuracy and flexibility needed for rapid prototyping or low-volume runs.
Electronics
Electronics and semiconductor industries benefit from wire EDM as well—especially when creating tooling or fixtures that require fine detail and dimensional control.
At Krukemeier, our team supports customers in all of these industries. Our EDM machine shop is built for high-stakes projects where precision can’t be compromised.
When to Use Wire EDM for Your Project
Not every machining job calls for wire EDM, but when it’s the right fit, it can make a big difference in performance, quality, and efficiency. So how do you know when to choose it?
Start with the material. If you’re working with conductive metals—especially hardened ones like tool steel, titanium, or Inconel—wire EDM is a strong option. Unlike conventional machining, EDM doesn’t rely on physical cutting tools, so it handles tough materials with ease and without introducing heat or distortion.
Next, consider geometry. Parts with fine slots, sharp internal corners, small radii, or complex contours are often difficult or impossible to machine using standard methods.
It’s also ideal for thin-walled parts, tight-tolerance components, and applications where burrs or tool marks aren’t acceptable. If the part needs to be both complex and consistent from one to the next, wire EDM is a smart choice.
Krukemeier often recommends this process for prototyping, short-run production, and high-precision applications across aerospace, medical, and defense. When traditional cutting can’t deliver the results you need, wire EDM fills the gap.
Why Choosing the Right EDM Machine Shop Matters
While the wire EDM process itself is powerful, the results depend heavily on who’s running the machines. Not all shops are built the same—and that’s especially true when it comes to tight tolerances and challenging materials. Choosing an experienced EDM machine shop can make the difference between a smooth project and a series of setbacks.
At Krukemeier, our team understands how to set up each job for success, whether it’s holding micron-level tolerances or optimizing the process for better speed and surface finish. We’ve invested in reliable equipment, proven methods, and a quality system that keeps every detail on track.
A qualified EDM machine shop knows how to balance precision with efficiency. That means helping you avoid costly rework, reduce lead times, and meet deadlines with confidence.
We also bring engineering expertise to the table. If you’re not sure whether wire EDM is right for your part, our team can guide you—explaining tolerances, material compatibility, and the best approach for your goals.
When accuracy matters, trust a shop that treats precision like a promise.
Is Wire EDM Right for Your Project?
If your parts require precision, consistency, and clean detail, wire EDM is worth considering. It’s especially valuable when working with conductive materials that are hard to machine, or when your design includes features that are too complex for traditional methods.
At Krukemeier, we help customers meet strict tolerances and avoid delays caused by secondary operations. Whether you’re building one prototype or producing a run of mission-critical components, we bring the focus and experience needed to get it right the first time.
We understand the importance of reliable tolerances, and we’ve built our EDM machine shop around delivering those results with speed and precision. From setup to inspection, every step is handled with care to ensure the finished part meets your exact requirements.
If you’re ready to simplify your machining challenges and raise the bar for accuracy, reach out. Our team is here to help you decide if our services are the right fit for your next project—and to deliver results you can trust.