Electrical Discharge Machining (EDM) is a precise way to remove material using tiny, controlled sparks. Ram EDM and Wire EDM offer distinct advantages depending on part geometry, material, and application. Knowing how they differ is helpful for engineers and manufacturers when picking the correct method for their projects.
Both methods are popular in aerospace, medical, and manufacturing industries, where precision is crucial. Choosing the proper EDM process can boost production efficiency, lower costs, and enhance the quality of the parts. Unlike regular machining, EDM works with conductive materials, making it a top choice for fields that demand high accuracy.
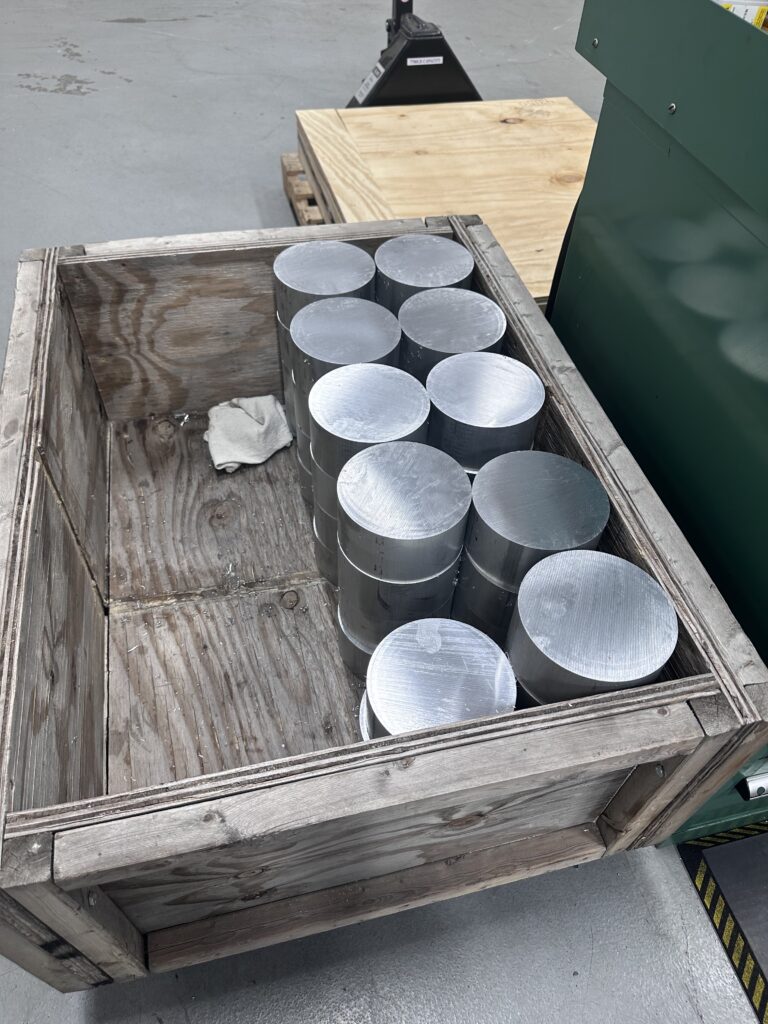
What is Ram EDM?
Ram EDM, also known as Sinker EDM, uses a custom-shaped electrode to erode material and create complex cavities. This method benefits parts requiring intricate, deep, or non-through features.
The process uses the electrical potential between the electrode and the workpiece. This creates controlled sparks that can remove material without actually touching it.
Advantages of Ram EDM:
- Ideal for 3D cavities: It’s best for molds, dies, and intricate shapes where wire cutting is not feasible.
- Works on hardened materials: Easily machines tough metals like Inconel, titanium, and hardened steel.
- No direct line-of-sight required: Can create blind holes, deep recesses, and sharp internal corners.
- Multiple electrodes for efficiency: Different electrode shapes allow high flexibility and consistency in machining.
- Excellent surface finishes: Can achieve smooth finishes with proper dielectric fluid and finishing techniques.
Common Applications:
Manufacturers rely on Ram EDM to produce injection molds and die casting components. The tool and die industry frequently relies on Ram EDM to form operations. The process is also suitable for EDM drilling, which enables precise hole creation in complex parts.
What is Wire EDM?
Wire EDM utilizes a thin, constantly fed wire electrode to cut through the material precisely. The process is similar to high-speed bandsaw cutting but uses electrical discharges instead of mechanical force. Wire EDM machining is particularly effective for cutting through conductive materials with minimal mechanical stress.
Advantages of Wire EDM:
- Superior precision: Achieves tolerances as tight as +/- .0005.
- Excellent for intricate shapes: Cuts sharp corners, fine details, and complex contours without distortion.
- Minimal material stress: No direct cutting force reduces mechanical distortion, making it ideal for delicate parts.
- Handles tough materials: Works efficiently with hardened steel, carbide, and superalloys.
- Efficient for multiple parts: Can stack-cut various pieces at once for higher production efficiency.
- Automated process: Wire EDM can run unattended once set up, improving cost efficiency.
- Common Applications:
- Aerospace manufacturers use Wire EDM for components that require extremely tight tolerances. In the production of medical implants that require intricate details, it is a preferred method.
Wire EDM is helpful in automotive tooling and prototyping because it offers amazing precision. It also works great for making precise gears, custom parts, and electrical connectors. This machining process ensures that even the most complex parts meet industry standards.
Choosing the Right EDM Process
The shape of the part is essential when choosing between Ram EDM and Wire EDM. Use Ram EDM for deep holes, complex 3D shapes, and internal features. Wire EDM works best for cutting detailed 2D profiles, sharp corners, and thin walls.
The type of material also affects the choice. Both methods can handle hardened metals. Still, Ram EDM is better for deep cuts in rigid materials. Wire EDM gives high accuracy and creates less stress. It is generally faster for cutting all the way through and for large production runs. Ram EDM takes longer, but it is necessary for shapes that Wire EDM cannot make.
Cost is another factor, as wire EDM is more affordable for complex 2D shapes and repeated cuts. Ram EDM needs custom electrodes, which can raise setup costs but are essential for deep cavity work.
Both Ram EDM and Wire EDM are key in precision machining. Choose Ram EDM for deep cavities or blind features. Choose Wire EDM for detailed profiles, fine details, and tight tolerances.